Precision CNC Machined Parts and Components for the Energy Industry
The energy industry is rapidly growing, with increasing demands for precision-machined and durable components across various sectors, including fossil fuels, solar, water, and wind energy. Equipment like drilling rigs, hydraulic fracturing systems, refineries, wind turbines, and solar panels all require components made from robust materials with tight tolerances. CNC machining is an ideal solution for the energy sector, enabling the production of high-quality systems and rapid, accurate repairs.
At TDB Machining Shop, we provide comprehensive machining solutions for the energy and renewable industries, delivering precision-machined parts built to perform reliably in harsh environments, including corrosive and abrasive conditions. Our skilled engineers and machinists have extensive experience in producing replacement parts for refineries and high-volume precision components for solar panels. We collaborate closely with you to ensure the production of top-quality components that meet your exact specifications.
Whether you need components for wind and solar power systems or hydropower turbines, we use the finest materials and maintain the tightest tolerances to deliver results you can trust.
Materials Available for CNC Energy Parts
Our team of skilled CNC engineers specializes in producing a wide range of parts for the energy industry. With expertise across various materials, we can create component parts tailored to your specific needs and applications. Some of the common materials we work with to manufacture components for solar panel and wind turbine producers include:
Metals
We work with a wide range of commonly used metal alloys, including aluminum, stainless steel, steel, copper, and titanium. These metals are ideal for applications requiring high conductivity, corrosion resistance, and lightweight strength. For instance, steel is often used for concentric pipes due to its toughness and durability, while copper is preferred for its superior electrical conductivity. Additionally, we offer other material options such as magnesium, brass, silver, tin, superalloys, and even custom materials tailored to meet specific project requirements.

Nylon & Thermoplastics
We specialize in producing high-quality machined components designed for both offshore and onshore applications. Nylon and other high-performance thermoplastics are particularly advantageous due to their strength, lightweight properties, corrosion resistance, and durability, making them ideal for demanding exploration and production environments. For example, nylon is often used in cable handling and clamping applications, while thermoplastics can be CNC machined to create high-performance components.
We offer a range of thermoplastic materials, including:
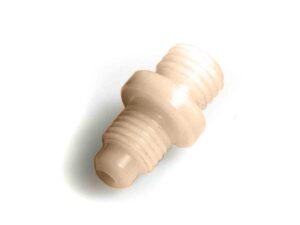
- Nylon 6 & 66 – nozzles, sheaves, wear pads, gears, industrial bearings
- HDPE – cut boards, covers, pyrotechnic purposes
- PEEK – seals and wears components, connectors, insulators, metal replacement
- ULTEM – insulators, analytical components, underwater connector bodies
- PPS – HPLC components, high-speed bushings, pump
- PVDF – chemical transfer pipes, piping, sheets, tubing, films, tank lining
- PAI – high-temperature electrical connectors, valve seats, wear rings, structural parts
- Other and custom options
Post-processing Available for CNC Energy Parts
We understand the importance of combining high-quality parts with a visually appealing finish. To meet this demand, we offer a variety of finishing options that can enhance the mechanical properties of your components. These finishes not only add a decorative touch but also provide functional benefits, such as improved durability, corrosion resistance, and wear protection, which are essential in the energy and power industries.
Here are some of the finishing options available for energy and power components:
- Plating
- Anodizing
- Passivation
- Heat Treatment
- Laser Engraving
- Painting
- Oxidation
- Chromate
- Electroplating
- Insert Installation
- Polishing
- Brushing
- Texturing
- Powder Coating
Advantages of CNC Machining for Energy Parts
Renewable energy projects depend heavily on advanced technology, equipment, and machinery to ensure smooth operations. These installations must achieve optimal efficiency and reliability to reduce their carbon footprint while maximizing power generation. To ensure long-term dependability, high-quality parts manufactured through CNC machining are essential in renewable energy projects.
Here are several key benefits of using CNC machining for part production in the renewable energy sector:
- CNC machining excels at producing intricate and complex components.
- It ensures parts have high-quality finishes and exceptional precision.
- The process is flexible, accommodating both large-scale production and small custom projects.
- CNC machining is versatile, producing parts of various sizes with consistent accuracy.
- It is cost-effective, especially for quick repairs or modifications to existing parts.
Applications of CNC Machined Parts for the Energy Industry
The energy sector demands high precision and strict adherence to specifications during manufacturing. Whether it’s solar, wind, or water energy, large parts and components must be durable and capable of withstanding harsh operating conditions. We are prepared to tackle the challenges across various energy sources, including commercial electricity, solar power, fossil fuels, oil, and gas, by offering comprehensive manufacturing solutions that enhance product quality and cost efficiency.
Some of the energy components we manufacture include:
- Gearboxes
- Jigs and fixtures
- Flowmeter parts
- Generator parts
- Quick repair tools
- Pilot testing parts
- Sand control screens
- Hangers
- Turbine blades
- Pump manifolds
- Drill rig components
- Nozzles and flow meter parts
- Engineering test pieces
- Flowline components
- Wind and water turbines
- Blades, rotor parts, and fans
- Impellers, pipelines, and pipe centralizers
- Power stations and transformer components
- Gears and shafts (ram shafts, locking shafts, and bonnets)
- Enclosures and sealing accessories for explosives and perforating
Why Choose Us for Energy Parts Production?
- Quick Quoting: Our efficient quotation system and prompt design feedback help you save time and reduce costs. Expect to receive a quote within 24 – 48 hours, often even sooner.
- Rapid Prototyping: Utilizing state-of-the-art CNC machines and a variety of auxiliary equipment, we provide continuous rapid processing for part prototyping and mass production of energy components.
- Custom Energy Parts: We specialize in creating tailored components that meet the specific needs of the energy, oil, and gas industries. Our solutions offer numerous opportunities for mechanical, cosmetic, or performance-driven customization.
- Competitive Pricing: Our on-demand production services for industrial components deliver cost-effective solutions. Our manufacturing capabilities exceed traditional methods in terms of cost efficiency, speed, and quality.
- Exceptional Precision: We possess the expertise to manufacture large parts with outstanding dimensional accuracy and tight tolerances. Our multi-axis CNC machines ensure precise production, while our skilled engineers and advanced machinery deliver the highest level of precision for your projects.
- No Minimum Order Quantity: At TDB, we offer the flexibility you need, whether you require a single part or a thousand. With no minimum order quantity, you can benefit from our low-volume production options, allowing you to manufacture prototypes or small production runs without limitations.
CNC Machining for Four Main Sectors in the Energy Industry
CNC machining is versatile and can be applied to almost any energy project. However, we specialize in four main sectors: hydropower, solar energy, wind energy, and oil & gas.
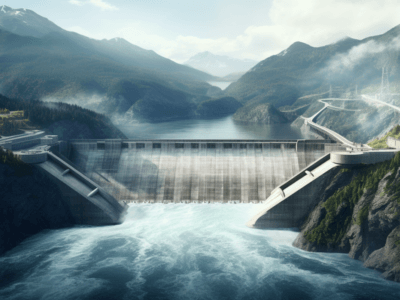
Hydropower
CNC machining is ideal for producing the large, precise, and durable components required in hydropower turbines. Parts such as shafts, bushings, turbine housings, impellers, and covers need to endure extreme pressure and corrosion, making stainless steel a common material for these applications. CNC machining handles these materials efficiently.
Many hydropower parts, like turbine components, can only be manufactured using CNC machines capable of handling larger dimensions. This versatility allows CNC machining to produce both large and small parts essential to keeping the operation of hydropower generators.
Solar Energy
CNC machines are increasingly favored for rapid prototyping of solar panels due to their flexibility in design modifications. As a result, panel manufacturers are relying on CNC machining centers to produce support components such as panel frames, back rails, and carrier rails, which require extensive cutting, milling, and drilling processes. Beyond the solar cells and frames, many additional parts related to the panel’s movement demand the precision that only CNC machining can deliver, ensuring efficient production and reliable performance in solar energy systems.

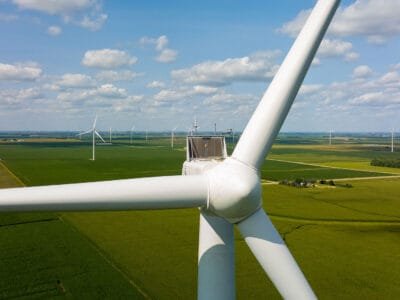
Wind Turbines
To generate wind power, parts must be both highly durable and precise. Beyond the turbine blades, CNC machining plays a crucial role in producing many key drive components located inside the turbine nacelle, such as main shafts, generator frames, brake components, hubs, gears, gearbox housings, rotors, and YAW system components. Additionally, CNC machining is vital for creating high-precision holes in the turbine’s heat exchange plates.
CNC machining is also ideal for manufacturing the large pitch bearings used in the blade angle adjustment mechanism. These bearings, requiring precise dimensions and high accuracy, are critical for optimizing the turbine’s performance and ensuring safety by adjusting blade angles according to changing wind conditions.
Oil & Gas
Components used in the oil and gas industry demand exceptional quality and precision. Given their prolonged operation and exposure to harsh underground conditions, strength, durability, reliability, and dimensional accuracy are critical to ensuring a long service life. CNC machining guarantees components with outstanding dimensional precision and tight tolerances. Additionally, our advanced CNC machines enable the production of large parts with high strength-to-weight ratios, making them ideal for fabricating ball valve balls, couplings, down-hole tools, pump components, pipes and fittings, fluid ends, feed fingers, and valve blocks.
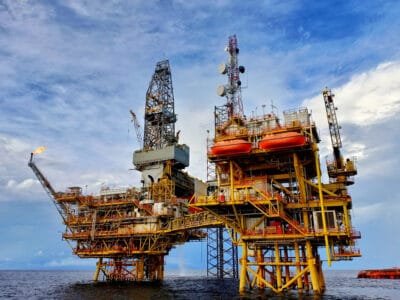
Prototyping CNC Machining Services for the Energy Industry
In the energy sector, CNC machining is indispensable across various industries, including hydropower, solar energy, wind turbines, and oil & gas. Precision machining is critical for manufacturing essential energy components, from wind turbine blades and rotor shafts to handling maintenance and repairs. When selecting a machining partner for energy-related projects, it’s crucial to choose a provider with proven expertise in the field.
At TDB, we deliver top-tier CNC machining services to companies worldwide, producing high-quality components for the energy sector. For precision-machined parts created by a team of trusted professionals, TDB is your ideal partner. Contact us today to learn more about how we can support your energy project with our advanced CNC machining capabilities.